In most vehicles on the road today, the driver's accelerator pedal sends an electrical signal to the engine control module (ECM). This signal is sent to an electric motor mounted to the throttle body.
The ETC valve opens proportionally to the accelerator pedal, allowing air to enter the engine. It also controls the flow of fuel, enabling a smoother, more powerful acceleration.
Control Strategy
Currently, the control strategy of an ETC Valve motor is based on a single proportional-integral-derivative (PID) controller to induce the throttle valve motor operation. However, non-linearities can be induced by the presence of mechanical spring system or other design attributes which can influence the throttle position in different areas away from a default valve position.
Hence, the control system strategy has to deal with these nonlinearities for reducing the position error of the throttle valve. Moreover, this nonlinear characteristic affects the system uncertainty which requires a separate control system in EMS strategy to handle these uncertainties for estimating the estimated opening angle of the throttle valve.
In this paper, two adaptive controllers named adaptive backstepping controller and adaptive sliding mode backstepping controller have been investigated for plate angular position control of electronic throttle valve. Both of these adaptive controllers are tuned on a try-and-error basis to achieve optimal performance and convergence rate.
PWM Control
PWM (pulse width modulation) is an excellent technique for controlling DC motors. This technique uses a switching transistor to provide the output voltage to the motor terminals, delivering it in pulses that keep the terminals either fully ON or fully OFF.
With this method the power loss is small and the amplitude of the output voltage remains constant. This results in a much more linear control of the motor, which means it can rotate much more slowly without stalling or overheating.
A good quality PWM fan will have special IC driver chips within the motor hub that generate a sloped PWM signal instead of a flat square one which tends to create unpleasant clicking noises when the fan is at low speeds.
If you're looking to get full bi-directional control then the only way is with a PWM Bi-Directional Controller. Fortunately, this gadget has all of the features you need at a price that's much less than most other automotive repair and diagnostic devices on the market.
Pulse Length
The pulse length of an ETC Valve motor is directly related to the switching frequency of PWM control. The higher the pulse frequency, the faster the switching is.
During switching, the leading edge of the course is characterized by shorter pulses. This is due to the smaller pressure differential on the venting valve.
In addition, the decreasing edge of the course is characterized by longer pulse durations than the leading edge. This is because the required filling or draining power depends on the size of the difference between the actual and the required pressure values, and on the proportional increase in that difference.
At the same time, a constant power regulation of the pneumatic valves in conjunction with the PWM control is applied to regulate the required and constant pressures. This results in a smoother regulation of the pneumatic valves at steady pressure, with no abrupt distortions.
Voltage
In an ETC Valve motor, the voltage is controlled by a PWM (pulse width modulation) signal. The resulting waveform is similar to that of a servo motor.
The pulsing current flows through the motor in a series, which results in the valve opening. The voltage is regulated to maintain a stable valve angle with a low voltage at the start of a stroke, then increasing to a higher voltage to open the valve more fully on the next stroke.
The ETC valve motor can also be given an interlock signal to operate a separate actuator elsewhere in a facility, such as if the main power on-site is interrupted. If this is the case, it may be necessary for the actuator to open the valve and place it in a safe position to avoid contamination or damage to other equipment.
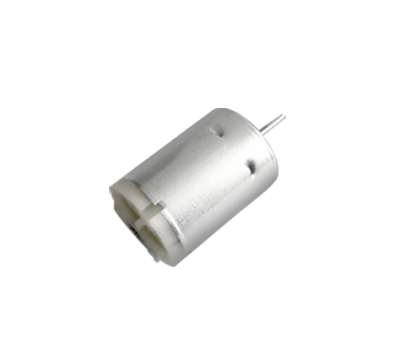
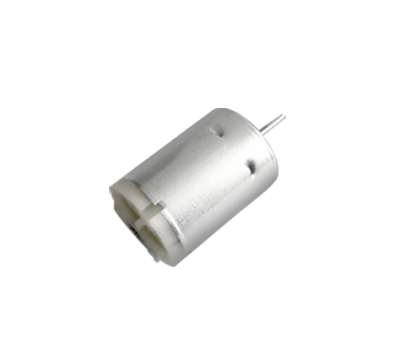